ALUMINUM COATING
FOR OPTICS AND TELESCOPE MIRRORS
Here is more information about our mirror coating.
Today we have a new 8 inch Pyrex telescope mirror to coat.
First I use a bit of paint thinner to remove any finger
prints and to remove pitch from around the edge if there is any.
Next I remove the paint thinner with semiconductor grade methanol. Methanol is the
same alcohol as in wood alcohol (don't drink this stuff).
Next I put the mirror into a plastic pan with warm 1/10 concentrated
HCl to soak for 10 minutes while the oil diffusion pump is heating.
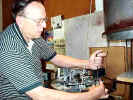
Picture 1 shows me installing a new tungsten filament.
Picture 2 shows the filament with the loops of
aluminum wire crimped onto it. The baffle box SiO
evaporator was full of ash so I dumped it out.
In picture 3 I am reinstalling the baffle box.
The next step would normally be done in a clean room
but we have learned to make do. I lay out the sheets
of Kimwipe paper for ready use. For the final cleaning
I use the methanol then dry with the Kimwipes.
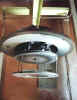
Picture 4 shows the 8 inch mirror being traversed
to the vacuum tank. Just before lowering the mirror
into the vacuum tank I huff the dust (if any) away
with an ear syringe. There are two mechanical vacuum
pumps. The large pump "roughs out" the tank while
the second pump backs the oil diffusion pump.
After three or four minutes the vacuum in the tank
is about 1/3 of one millimeter of mercury (there
being 760 millimeters of mercury in one atmosphere).
After pumping for three or four more minutes both
mechanical pumps are valved to back the diffusion
pump and the large poppet valve between the diffusion
pump and the tank is opened slowly and carefully so
as to avoid a stall in the diffusion pump.
After 20 minutes the vacuum in the tank is about .00001 millimeters of mercury. The mirror rotator
is started and the aluminum is evaporated from
the tungsten filament using a low voltage, high
amperage power supply. The aluminum coats every
thing in the tank that is visible from the filament.
People have asked me if the coating will cover
scratches on the mirror. No, the coating is only waves of light thick. See
Note. ( Don't worry about the scratches, the mirror
figure is the most important thing ).
Next the baffle box leads are connected and the
SiO is evaporated. SiO2 (quartz) cannot be
evaporated except by using an electron beam and
then it will break down to SiO.
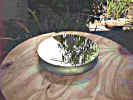
Picture 5 shows the finished mirror coming out
of the tank. I wrap the mirror and stamp the date on the
back. Some mirror makers tell me "Now I'm
going home and build the telescope". I don't
like to hear this since the chance of building
the telescope without damaging the coating
seems remote to me. Better to build the telescope
before figuring the mirror and use the telescope
for testing the mirror while figuring. Bright objects like the moon will look great
even with the mirror uncoated.
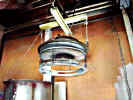
The picture at left shows a small cassigrain secondary being
attached to its backing plate after re-coating. The main mirror holder will hold a 20 inch mirror.
With an adapter we have done many 18 3/4 inch porthole
mirrors. In the last picture you see the large adjustable mirror holder. This swing arm adapter
will
adjust from 18 1/2 inch to 11 1/4 inch.
Coating Thickness Note
It is possible to get an idea of the coating thickness from
the quantity of aluminum evaporated. Four one gram loops of aluminum are
evaporated. The radius to the mirror is about 15 inches. If the aluminum
goes equally in every direction then the four grams would be spread onto the
inside of a sphere of radius 15 inches. The surface of a sphere
equals Pi R2 times 4.
15 inches equals 38.1 centimeters. 38.1 * 38.1 =
1451.61.
1451.61 times Pi equals 4560.36 times 4 equals 18241.45 cm2.
Four grams divided by 18241.45 cm2 equals
.00021928 grams per square cm.
If the inside of the sphere were coated with water the water would be .00021928
cm thick
and weigh .00021928 gram.
The aluminum weighs 2.7 grams per cubic cm.
So .00021928 gram divided by 2.7 gram/cm equals .0000812148 cm thick.
The wave length of green light is .00053 millimeters.
So 0.000812148 mm coating thickness divided by .00053 mm per wave equals about
1.53
waves. If two loops of aluminum were evaporated a partial mirror with a
transmission of about optical density 3 ( 1 / 1000 ) would be formed.
The thickness of the 'quartz' overcoat is measured by watching
the color rings on the side of the chamber about 2 inches from the
evaporator. As the SiO is evaporated you see a straw colored area near the
evaporator. In the center of the straw colored area alternate cyan and
magenta ring form as the SiO is evaporated. In total, eight magenta rings are
evaporated. At the distance of the mirror this is about 1/4 wave
thickness.
It
is also possible to coat plastic ( or even vacuum grease ) with aluminum.
In this picture we have just coated three plastic hemispheres for use in a 360
degree camera.
March 26, 2007